- Convex And Concave Mirrors
- Convex And Concave Turning The Mechanics
- Concave And Convex
- Convex And Concave Definition
- Convex And Concave Turning The Mechanical
(a)Explain why t (1=t)uTuis a concave function on domf. Use convexity of the quadratic over linear function. (b)From this, show that log(t (1=t)uTu) is a convex function on domf. (c)From this, show that fis convex. 2.4 A quadratic-over-linear composition theorem. Suppose that f: Rn!R is nonnegative and convex, and g: Rn!R. You are provided with a convex mirror, a concave mirror, a convex lens and a concave lens. You can get an inverted image from (a) both the concave lens and convex lens. (b) both concave mirror and convex mirror. (c) both concave mirror and convex lens. (d) both convex mirror and concave lens. Soln: The answer is (c) both concave mirror.
Convex And Concave Mirrors
Description
This section is from the book 'Things To Make In Your Home Workshop', by Arthur Wakeling. Also available from Amazon: Things to Make in Your Home Workshop.
As soon as the amateur wood turner has learned how to turn a cylinder and make shoulder and taper cuts, he is ready to undertake ornamental work that requires concave and convex cuts.
do ornamental work.' src='images/Two-simple-exercises-in-making-concave-cuts-Once-mastered-t.jpg' height='296'>Fig. 22.- Two simple exercises in making concave cuts. Once mastered they give the wood turner power to<> do ornamental work.
To practice making concave cuts, first turn a cylinder 1½- in. in diameter and 8 in. long and lay it out as shown in Fig. 22 at the top. Set the calipers to 1/16 in- more than the smallest finished diameter and cut down with the parting tool at the center of the curves. Use the round-nose chisel for making the concave cuts and hold it perfectly flat on the T-rest (see Fig. 23). Begin the cuts a little inside the lines and gradually work down to the bottom of the cuts made with the parting tool.
Fig. 23. - Above: A round-nosed turning chisel held flat on the T-rest is used for shaping concave surfaces. Below : How the round-nose and diamond-point chisels are manipulated.
Another exercise is shown at the bottom of Fig. 22. Use a cylinder with shoulder cuts made as suggested in Fig. 9 and lay off the measurements indicated in Fig. 22. Make the concave cuts with the round-nose chisel. The supplementary exercise, Fig. 24, is designed to give practice on curves of longer and shorter sweep.
Convex cuts come next. Turn a cylinder 1 ½ in. in diameter and 8 in. long, lay out measurements according to Fig. 25 at top. Make small V-cuts with the diamond-point chisel. Round off the sharp corners with the diamond-point or skew chisel. For a second exercise (Fig. 25 at bottom) lay out a cylinder as shown and cut down to the smallest diameter with the parting tool; then round off the corners with the diamond-point (see Fig. 23) or the skew chisel.
Fig. 24 - A design which combines the two exercises shown in Fig. 22.
Fig. 25. - Useful exercises in making beads, which are frequently used in ornamental wood turning.
Beads of different diameters, such as the ones shown in Fig. 25 and on the supplementary exercise, Fig. 26 at top, are used extensively on turned work. It is therefore important to be able to make smooth and well-rounded beads. Specially shaped turning chisels, called beading tools, from 1/8 to 5/8 in. in width, can also be obtained and used for this purpose.
For the purposes of illustration, each of the preceding exercises has been designed to deal with only one type of cut. In most turned work, however, two or more of these cuts are combined, as in the simple projects illustrated at the bottom of Fig. 26 and in Figs. 27 and 28.
Chisel handles are of two kinds. One type, illustrated in Fig. 26, is tapered to fit into the socket of a chisel. As these tapers vary, it is necessary to verify or change the dimensions of the taper, as the case may be.
It should be remembered that the smaller end of all turned work should be run on the dead center, so that the end may be squared or rounded more easily and safely. In this case, therefore, the tapered end of the handle should run on the dead center. As the hole made by the dead center will not be objectionable in the finished product, it is better not to cut it away.
Fig. 26. - Above : Another exercise in turning. Below : A tapered handle for a socket chisel.
It is recommended to turn the taper first. The stock may be removed from the lathe and tried as often as necessary, until it fits the socket. The rest of the handle is then finished in the usual way, the concave part with the round-nose chisels and the convex part with the diamond-point or the skew chisel. The three lines on the handle near the end are cut for ornamentation. They are made with the point of the skew chisel.
Convex And Concave Turning The Mechanics
Fig. 27. - A time-honored wood turning: project - a stocking darner with a springy steel clamp for holding the stocking in place.
The other kind of chisel handle is for the tang type of wood chisel. Each handle is fitted with a brass ring called a 'ferrule,' which prevents the wood from splitting when the tang of the chisel is driven into the handle. Ferrules can be bought in different diameters, according to the size of the chisel. They should fit so tightly on the chisel handle that they must be driven in place with a mallet. All handles should be sandpapered as smooth as possible.
When sanding in the lathe, it is best to remove the T-rest. The sandpaper is folded into narrow strips and moved rapidly back and forth over the work. If it is held in one place, rings will appear on the object being sanded. Care should be taken not to round sharp edges. When the tools are kept sharp very little sand ing is needed. Ordinarily sandpaper No. ½ or 0 and No. 00 should be used.
Stocking darners are made in many different shapes. The one illustrated in Fig. 27 may be made in either one or two pieces. A clamp may be made out of an old clock or phonograph spring and fitted around the head of the darner. This will hold the stocking tightly over the convex face during the darning process. If the ends of the spring are heated, they may be bent as shown. The edges should be smoothed with file and emery paper.
Fig. 28. - A design for a hickory mallet, which will give beginners good practice in accurate turning.
The mallet, Fig. 28, is a serviceable tool for any woodworker. It is made in two pieces. The end of the handle entering the mallet head should be turned very accurately to the diameter indicated. To do this, a gage is made by boring a 13/16-in. hole in a thin piece of wood. This gage may be hung on the dead center while the handle is being turned, so that it is not necessary to remove the stock when testing.
Fig. 29. - A tilt-top table with a turned column. The top is decorated with an inlaid insert and border.
When the head has been turned to size, the exact center between the ends is measured and a line marked around the head at this point. Wrap a narrow strip of paper around the mallet head on this center line and cut it so that the two ends just meet. Remove the paper and fold it once. Wrap it around the mallet head again and mark a point on the center line at each extremity of the folded paper. These points, directly opposite each other, indicate the centers of the hole to be bored for the handle. The hole should be bored halfway from each side in order to get it true. If the halves should not meet exactly in the center, any unevenness may be removed with an inside-bevel gouge.
The mallet head may be held between the lathe centers or in a vise while the hole is being bored. In any case it is well to have someone 'watch' the bit to see that it is held horizontally and parallel to the ends of the mallet head.
Before joining the pieces, the end of the handle should be split along the center with a hack saw. When the handle and head are ready to be glued together, a wedge is made and driven into this saw cut. The end of the handle may be allowed to project a little, or it may be cut off flush with the head. Hickory is the best of the commonly available woods for this project.
Fig. 30. - Elevation and partial top view of the table shown in Fig. 20 ; details of the leg joint and top brace.
Continue to:
- prev: First Steps In Turning
- next: Small Table
Concave And Convex

Convex And Concave Definition
Convex And Concave Turning The Mechanical
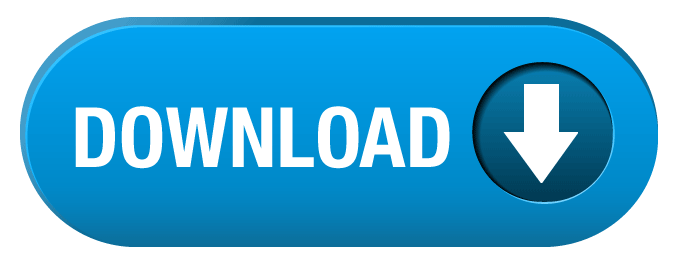